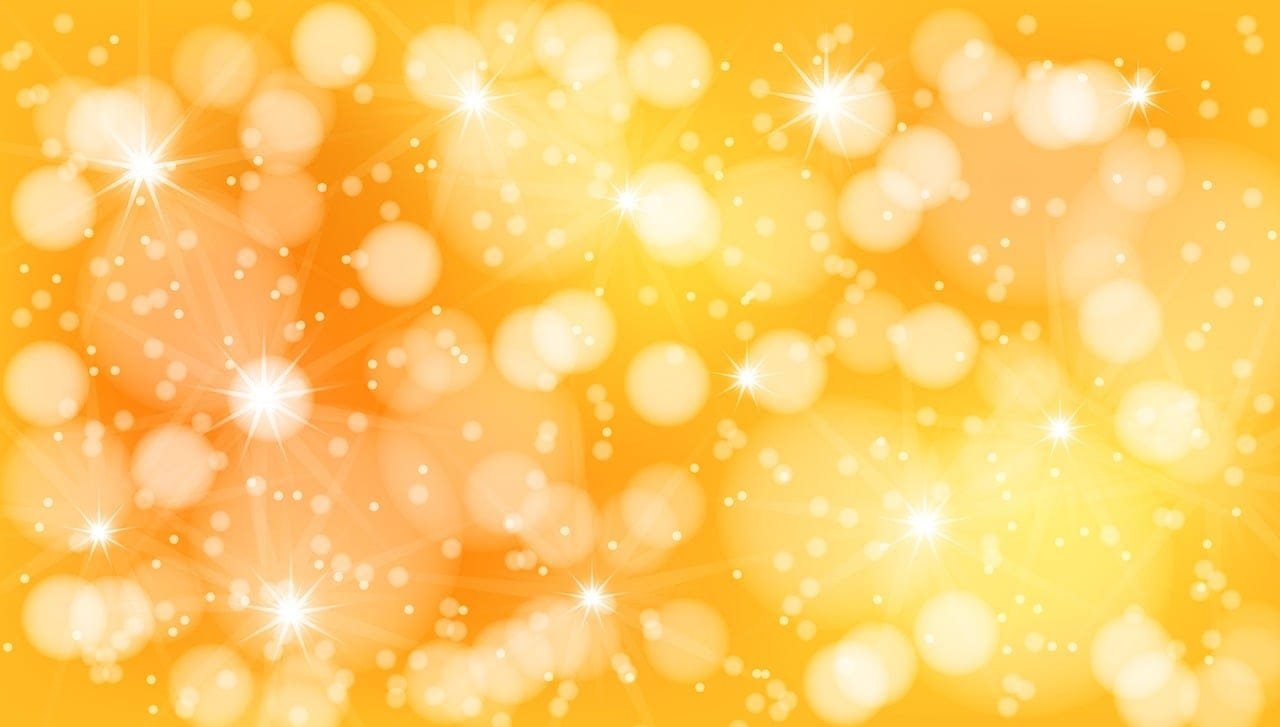
Management – Execute Correctly
“Management is doing things right; leadership is doing the right thing.” – Peter Drucker1
What is Management?
Management is the disciplined practice of transforming vision into reality. While leadership ignites the vision, management ensures its execution by coordinating tools, time, people, and resources to deliver value.
Work-Management, Management Controls, Supply Chain, Customer Service, Supply Chain Management Integration, Risks, and Managing Black Swans are all examples of management skills and expertise. Management is the discipline that is required to bring the planned physical product or service into existence. You can find a synopsis of management in the embedded video.
Historically, even early humans practiced forms of management by gathering materials for tools, collecting firewood, and prioritizing survival methods. As societal complexity grew, so too did the need for structure, strategy, and effective execution, marking the inception of management.
In contemporary settings, management encompasses diverse areas such as Work Processes, Supply Chain Integration, Risk Management, and Black Swan Navigation—all with the objective of efficiently and effectively bringing ideas to fruition.
From Vision to Execution
Leadership determines the right thing to do, while management ensures it is executed correctly. This relationship is akin to the www.SpiralInfluensa.com Model:
Leadership corresponds with Spiritual (Si) and Emotional Intelligence (Ei), focusing on vision and people.
Management corresponds with Cognitive (CiMi) and Logical Intelligence (Li), focusing on processes, control, and outcomes.
Together, these elements facilitate the transition from Direction (IS) to Execution (PS) across Micro, Meso, Macro, and Global levels.
Understanding Control vs. Controls2
Subject | Controls (Logistics) | Control (Orientation) |
Synonym | Measurement & Information | Direction |
Purpose | A means | An end |
Focus | The past & present | The future |
Nature | Analytical | Normative (What ought to be) |
Controls help track what is. Control guides what should be.
7 Golden Principles of Effective Controls
To empower Control (i.e., strategic direction), your Controls must be:
Economical – Cost-effective and efficient.
Meaningful – Reflect what truly matters (e.g., customer needs).
Appropriate – Aligned in precision with what’s being measured.
Congruent – Consistent with enterprise goals.
Timely – Neither too early nor too late.
Simple – Easy to understand and apply.
Operational – Actionable insights, not just reports.
Why Controls Alone Are Not Enough
Controls are neutral—they don’t guarantee success unless anchored in purposeful control. Poorly designed controls can mislead, while well-crafted ones provide clarity and momentum. Controls must:
Deliver results — in profits, performance, and customer satisfaction.
Measure both quantifiable and qualitative outcomes.
Be designed to trigger action, not just information overload.
The Management Toolbox
Execution depends on systems. One of the most powerful: the Supply Chain.
Figure 1: Supply Chain Flow
From Suppliers → Manufacturers → Distributors → Customers With materials flowing forward and information flowing backward, managing this cycle well is a hallmark of good management.
Figure 2: The House of Supply Chain Management
Foundation: Logistics, marketing, organizational theory, purchasing.
Pillars:
Integration – Great leadership, partners, collaboration.
Coordination – Strong planning, IT, process orientation.
Roof: Customer care & competitiveness.
Supply chains aren’t just operations—they are strategic tools for value creation.
Stay tuned for the next section: Supply Chain – The Engine of Execution.
Supply Chain: The Flow That Powers Everything
What is Supply Chain Management (SCM)?
Supply Chain Management (SCM) is more than logistics—it is the living pulse of value creation. As M. Christopher defines it:
“Supply Chain Management is a network of organizations that are involved, through upstream and downstream linkages, in the different processes and activities that produce value as products and services in the hands of the ultimate consumer.” — M. Christopher, Logistics & Supply Chain Management, p.153
This dynamic system connects ideas, inputs, resources, operations, partners, and technologies to generate a flow of value—transforming effort into customer experience.
Figure 1: Example Supply Chain Flow
Figure 1: Supply Chain Example (Courtesy: Hartmut Stadtler)4
Supply Chain Example (Courtesy: Hartmut Stadtler) diagram showing a series of supply chain steps: Suppliers, Manufacturing Firm, Distribution (Third Party), and Ultimate Customers. Materials flow from suppliers towards customers, while information (including demand) flows from customers towards suppliers.

Adapted from Stadtler & Kilger, this model reveals a layered flow of operations and decisions—converging and diverging across stages—not confined to a single company but formed as a value-generating network.
The House of Supply Chain Management
Inspired by Stadtler et al., the “House of SCM” is a symbolic architecture where:
The roof symbolizes Competitiveness—the ultimate goal.
The foundation is Customer Service—the essential means.
The pillars include Integration, Coordination, and Technology—each strengthening the system.
1. SCM Integration: Building Strong Partnerships
Integration begins with choosing the right business partners—those with synergy potential for mid- to long-term collaboration. Integration entails:
Partnership Formation: Selecting suitable partners based on aligned values and mutual strengths.
Network Organization: Legally distinct entities operating in a cohesive, collaborative system.
Strategic Alignment: Practicing inter-organizational leadership to harmonize shared vision and objectives.
This is where assessing partners’ alignment with the enterprise’s values and desired impact becomes vital.
2. SCM Coordination: Orchestrating the Flow
Coordination is the art of synchronization—ensuring all components move in harmony. It rests on three major elements:
• Information & Communication Technology (ICT)
Advances in ICT have revolutionized SCM. As Stadtler notes:
“Advances in information technology made it possible to process information at different locations in the supply chain and thus enable the application of advanced planning.”
Tools like ERP systems empower precision, responsiveness, and efficiency, turning SCM into a strategic asset.
Figure 2: House of SCM (Supply Chain Management) (Courtesy: Hartmut Stadtler)5
House of SCM (Courtesy: Hartmut Stadtler) diagram showing a house example of one foundation, two columns, and one roof. The foundation represents logistics, marketing, operation research, organizational theory, purchasing, and supply. One column is integration (including leadership), and the second is coordination (including planning). The roof represents customer care and competitiveness. This implies that the supply chain creates competitiveness from best customer service because of best integration (best leadership, collaboration, & partners) and coordination (plan, process orientation, and using IT). Logistics, marketing, operation research, purchasing, and supply support these.
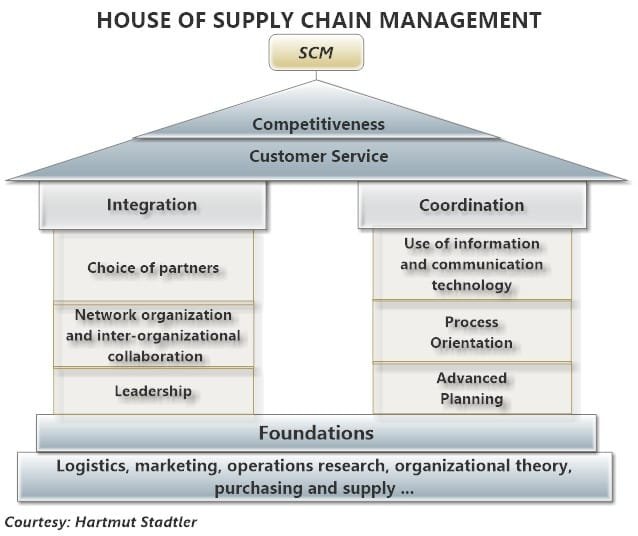
• Process Orientation
Aligning all functions around the customer journey ensures seamless execution—from order to delivery. It connects with Business Process Re-engineering (BPR) already discussed in System Logistics.
• Advanced Planning
Smart forecasting and demand-supply matching—especially with AI and analytics—enable proactive decision-making rather than reactive fire-fighting.
Customer Service: The Core of SCM
Without customers, supply chains lose their meaning. Drawing from LaLonde and Zinszer, customer service in SCM includes:
Pre-transaction: Understanding customer dreams and perceived value (via Madison Avenue Techniques—“people buy imagined experiences”).
Transaction: Fulfilling those dreams through delivery, service, and performance.
Post-transaction: Gathering feedback and improving experiences—creating a loyalty loop.
Customer Service is not a department. It’s the purpose.
Integration: The Engine of Long-Term Success
SCM is a shared journey. True integration requires:
Partner Selection: Aligning roles across three categories:
Competency-based internal alignment.
Standardized, low-variation outsourcing.
High value “Make or Buy” decisions.
Network Organization: Creating “virtual companies”—dynamic networks that operate with unity while preserving autonomy.
Leadership: Cultivating shared direction, mutual respect, and strategic collaboration across legally distinct entities.
Coordination Revisited: Flowing Together
SCM success depends on the triple coordination of:
Information (via ICT),
Materials (logistics),
Finances (value exchange).
Synergy is the thread tying them together. These flows drive agility, competitiveness, and resilience.
Risks in Supply Chain: Managing the Unseen
In the real world, disruption is not “if”—it’s “when.” Risks compromise control, collapse systems, and destroy value—unless managed proactively.
Three Risk Categories:
Known Risks Predictable and regular: insurance renewals, contracts, etc. These can be planned and benchmarked.
Known–Unknown Risks Events that have a history, but uncertain timing and impact: economic shifts, regulatory changes, etc.
Unknown–Unknown Risks (Black Swans) Unthinkable and unforeseeable. Sudden. Extreme. Devastating—or occasionally, game-changing opportunities.
Black Swans6: Prepare for the Shockwave
Drawing from Nancy Green’s7 survivor psychology, a resilience-first approach is adopted.
What to Do When the Storm Hits?
Detach Emotion: Leadership must remain rational, activating personal influence strategies to restore clarity and direction.
Realignment: Black Swans crush individual and public spectrums. Regular recalibration boosts shock-resilience.
Preparedness Over Prediction
We can’t always see the wave—but we can learn to surf.
Black Swan preparedness isn’t about guessing the event. It’s about:
Training minds to detect trends,
Building systems that can pivot,
Strengthening individuals to lead under pressure.
Final Thought: Supply Chain is the Lifeline of the Ultimate Enterprise
Within the framework, supply chain isn’t just a function—it’s a flow. A living system that connects purpose, people, and performance. When aligned with multiple intelligences, the supply chain becomes more than efficient—it becomes resilient, meaningful, and transformative.
Final Thought: Management, The Realization of Imaginations
Management is the bridge between ideas and impact. It takes the intangible (aspiration, intention) and shapes it into tangible results (products, services, value). Management is seen not just as a discipline, but as a manifestation of intelligence—cognitive, moral, and logical—working in harmony to serve the greater enterprise mission.
- https://informalcoalitions.typepad.com/informal_coalitions/2007/02/drucker_on_cont.html ↩︎
- https://informalcoalitions.typepad.com/informal_coalitions/2007/02/drucker_on_cont.html ↩︎
- Martin Christopher, Logistics and Supply Chain Management. Strategies for Reducing Cost and Improving Service, ©1998Financial Times, Pitman Publishing, London ↩︎
- Martin Christopher, Logistics and Supply Chain Management. Strategies for Reducing Cost and Improving Service, ©1998Financial Times, Pitman Publishing, London ↩︎
- Hartmut Stadtler, Christoph Kilger (Eds.), Supply Chain Management and Advanced Planning Concepts, Models, Software and Case Studies, Third Edition, ©Springer Berlin Heidelberg 2000, 2002, 2005 ↩︎
- http://www.aon.com/attachments/risk-services/Manage_Black_Swan_Even_Whitepaper_31811.pdf ↩︎
- http://www.aon.com/attachments/risk-services/Manage_Black_Swan_Even_Whitepaper_31811.pdf ↩︎